What is SLS?
Selective Laser Sintering (SLS) is the ideal technology for entering the world of additive manufacturing.
Production is fast and precise using this method. Faithful prototypes, precise end-use pieces, breathtaking geometric shapes or shapes not yet manufactured using conventional technologies are all easily tested in practice and compared to your expectations.
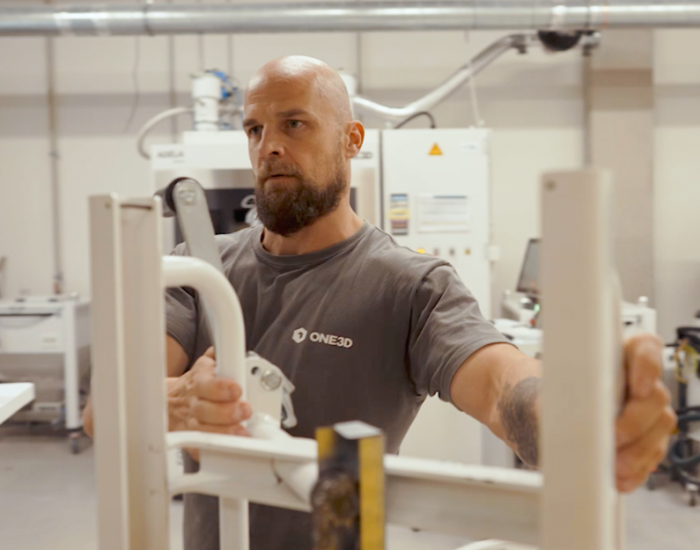
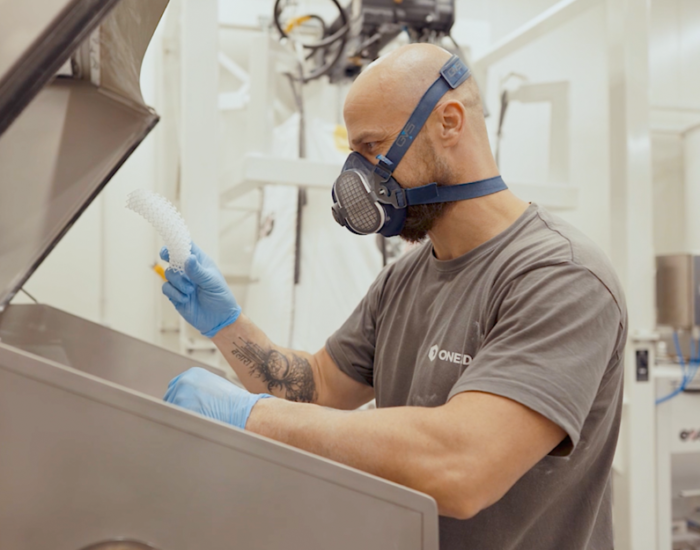
Suitable use of SLS
Rapid prototyping and low-volume, phase-in or custom production of end-use parts. Thanks to the flexibility and wide portfolio of proven materials, you can’t go wrong
with SLS.
Are you looking for a reliable technology that offers a wide portfolio of production materials, with a guarantee of excellent mechanical properties and the possibility
of prototype and small volume production? Choose SLS.
Main advantages
- great ratio of price to acquired properties
- good mechanical properties and chemical resistance
- no need for additional support of the part
What does the use of SLS technology look like in healthcare and the automotive sector? You can learn from our case studies. We used SLS to manufacture
orthotic helmets for newborns or air distribution for Škoda cars.
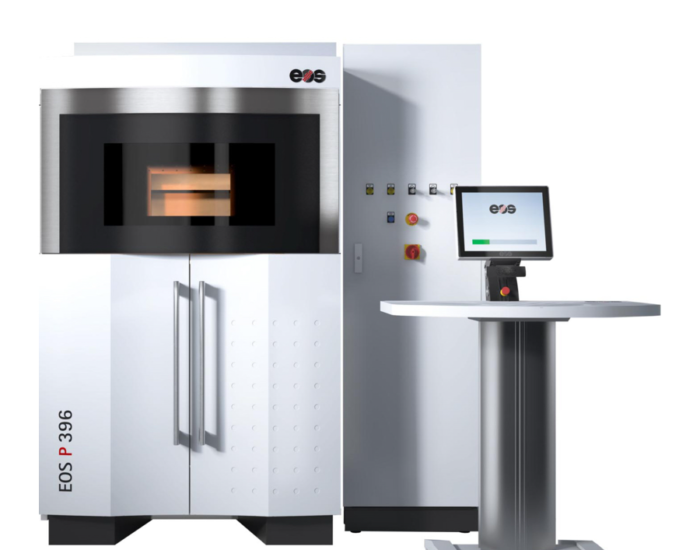
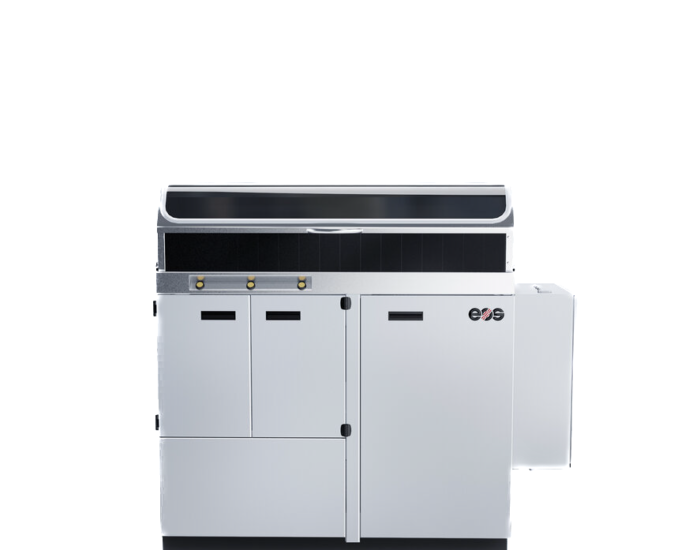
Technical specifications
Standard delivery time | minimum of 4 working days (depends on material selection, size and number of parts and surface finish) |
Standard accuracy | according to ISO 2768-c |
Layer thickness | 0.12 – 0.15 mm |
Minimum wall thickness | 0.5 mm (depends on material, lower thicknesses can be produced after consultation) |
Production chamber size | 340 x 340 x 600 mm (part size is theoretically unlimited as the part can be “cut” by software and glued together after production) |
Surface characteristics | The part typically has a grainy surface that can be treated by abrasive blasting, dip dyeing, chemical smoothing, spray painting, plating or machining. |
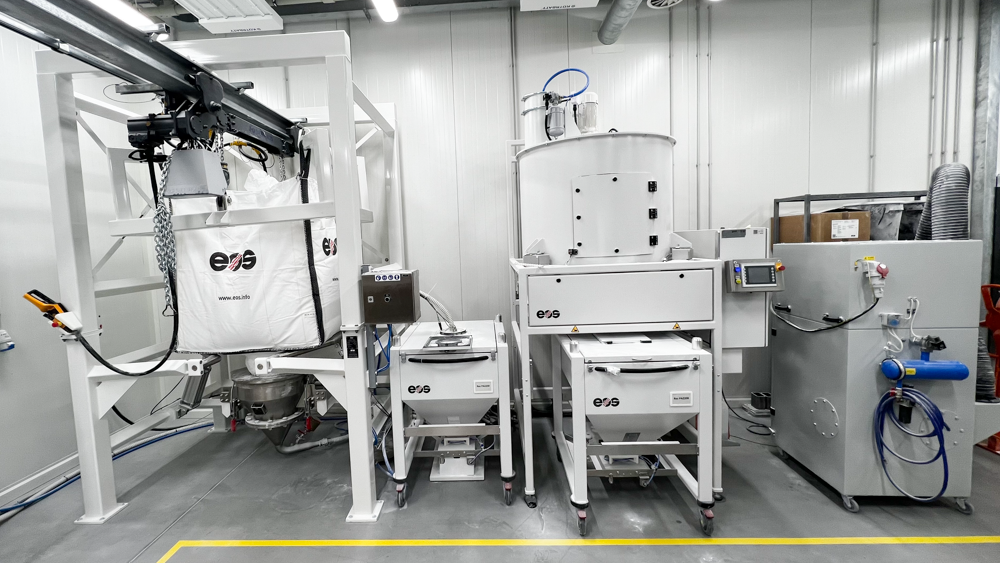
How SLS works
SLS uses a CO2 laser to produce parts, which, on the basis of a computer 3D model, sinters the polymer powder into the desired shape. The entire process takes place in a production chamber, in which the powder is gradually applied over the entire surface
in layers.
The laser bakes and cures precisely defined areas in each layer according to the cross-sectional shape of the part. All the surrounding powder, which serves as a support for the fired part throughout, remains unchanged and is fully recycled after the manufacturing process is completed.
Recoating
Before production begins,
the machine chamber is flooded with inert gas, making the production parameters more stable and the parts produced less porous.
Preheating of the layer
The delivery recoater applies a thin layer of powder over
the entire surface, which is heated with an infrared lamp just below the melting temperature of the polymer powder.
Sintering
The laser then burns out
the cross-sectional contour
of the part, which selectively sinters the powder, i.e. melts the material particles
and connects them.
Then the cross-sectional interior of all parts is sintered.
Lowering of the platform
After one complete layer
is completed, the production platform drops
by the thickness of the part layer and the whole process
is repeated until all parts
are manufactured.