Chemical smoothing of additive manufactured polymers lowers their surface roughness. The final roughness is approximately 3 times lower than before smoothing (see article). Lower surface roughness has many advantages, such as lowering friction and pressure losses, creating a glossy appearance, enhancing color hues, lowering water absorption and making the part surface easier to maintain. Materials used with powder bed fusion technology can then appear like parts manufactured using conventional technologies, as you can see in the image below.
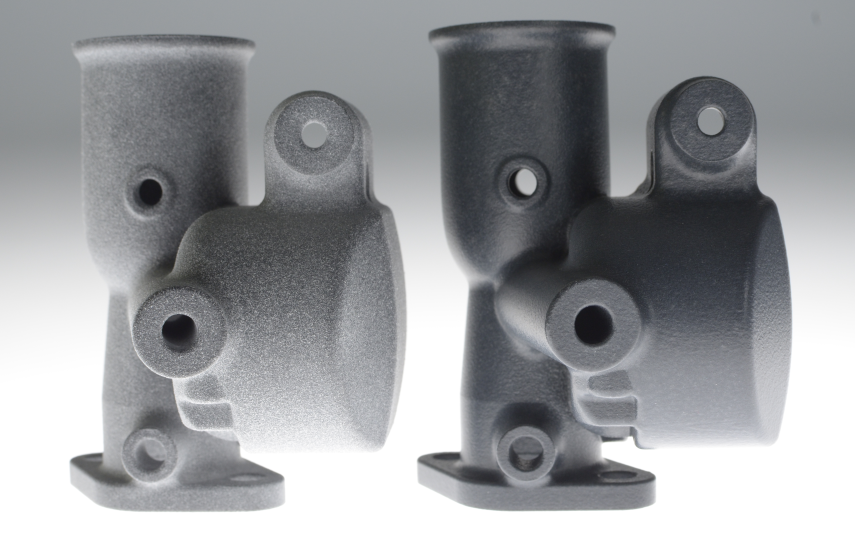
Fig. 1 Part made of PA12 (MJF) without processing (LEFT) and after smoothing (RIGHT)
This technology is applicable to a wide range of materials. Beside thermoplastics (e.g.: PA, ABS or PC), it is compatible also with thermoplastic elastomers (e.g.: TPE, TPU or PEBA). Besides pure polymers, it can also be applied to the surface of composite materials with additives, e.g. glass and carbon fibers or fire retardants. The advantages are many. But what happens to the mechanical properties of parts which undergo this type of processing? For demonstration, we have performed a total of 8 tensile tests of ISO 527-2 1A (4 mm thick) solids. Each value then represents the average over four measurements. As you can see in the table below, in the case of thermoplastics, no significant alterations occur.
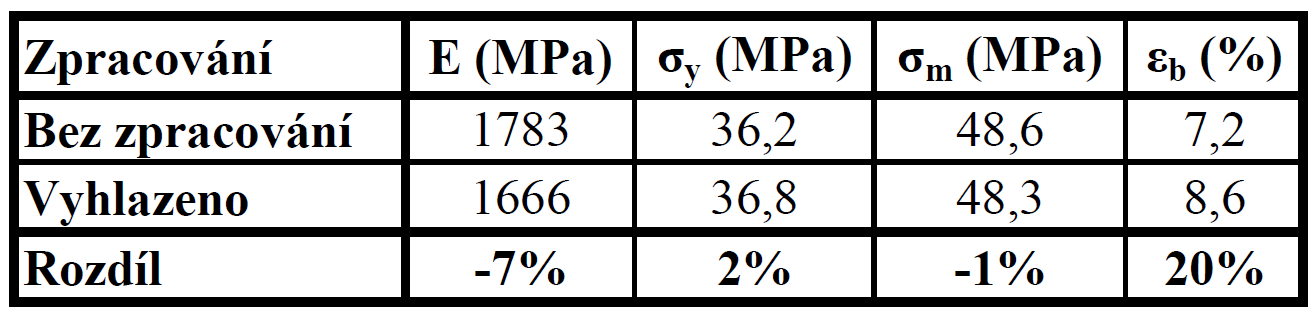
Tab. 1 Tensile test results, material PA12 (MJF) // E – modulus of elasticity; σy – yield point; σm – tensile strength; εb – elongation at break
One of the changes observed is roughly a 7% decrease of modulus of elasticity of the material (E). To achieve the same deformation as with the raw material, the smoothed test solid requires tensile stress about 7% lower. This change of rigidity is small enough to be considered insignificant.
The main advantage, as far as mechanical properties go, is the increase of elongation at break (εb), roughly by 20%. In practical terms, this means that material such processed will deform 20% more before a break occurs. The design engineers can use this to their advantage, in some applications. Surface smoothing will significantly minimize imperfections, which can cause local concentration of stress under load and thus also reduced elongation at break.
Fig. 2 Tensile test of a chemically smoothed sample, material PA12
It must be said, though, that changes are significantly reliant on the geometry of a given part. Parts with thin walls will be affected more than parts with thicker walls. The results are valid for test bodies with thicknesses of 4 mm and as such may serve as a good general reference. Other than that, the effect smoothing has on mechanical properties also depends on the chosen parameters of the smoothing process.
By using different parameters, it is possible to achieve a different final appearance and surface roughness. For the most consistent smoothing of surfaces, it is appropriate to design the part in such way that the individual elements of the part would all maintain a uniform wall thickness or as close to it as possible.
Do not hesitate to contact our team and ask about your specific application.
ONE3D